8 Crucial Enclosure Design Considerations for Electronics & Industrial Equipment
- Outdesign Co.
- Oct 1, 2023
- 4 min read
Updated: Jan 19, 2024
Designing enclosures is a critical aspect of creating electronic devices, machines and systems. These systems or machines could be various testing & measuring equipment, medical devices, consumer electronics, diagnostic equipment and so on.
The product enclosures serve to protect sensitive electronic components from environmental factors, physical damage, and electromagnetic interference while also providing visually appealing aesthetics, user interfaces and access points.
In this article, we have listed 8 key design considerations for designing enclosures for various electronic devices and industrial equipment.
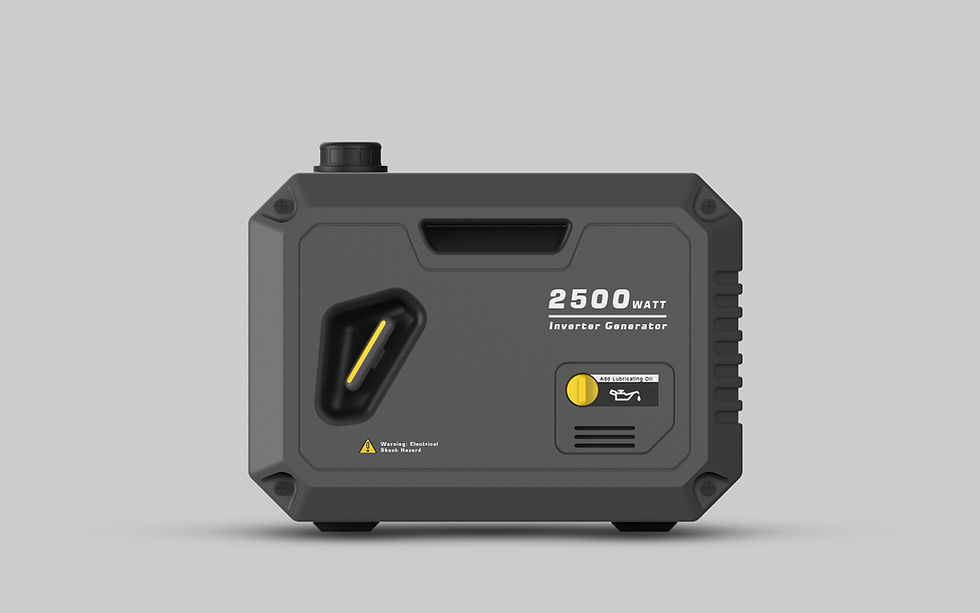
Image: Enclosure design by Outdesign Co - A product development company helping clients across 15+ countries to design & develop sleek new products, especially enclosures. Get in touch now.
1. Environmental Protection:
The environment in which the device needs to operate is an important consideration for the enclosure design. Apart from structural rigidity to withstand physical impacts and vibration, there are few other important considerations.
IP Rating: Determine the level of protection required against dust and moisture by using the appropriate Ingress Protection (IP) rating. This helps ensure the enclosure can withstand the intended environmental conditions.
Chemical Resistance: Consider the potential exposure to chemicals or corrosive substances in the operating environment and choose materials that resist corrosion.
Weather Resistance: Account for specific weather conditions for enclosures mounted outdoors and are directly exposed to the elements. Factors like UV-resistant materials, measures to prevent condensation inside the enclosure, provide drainage, anti-icing and snow shedding designs to prevent the buildup of ice and snow for colder climates.

2. EMI/RFI Shielding:
Sensitive electronic components need to be protected from electromagnetic interference (EMI) and radio-frequency interference (RFI) by incorporating conductive materials (like aluminum, steel) and shielding techniques in the device enclosure.
If the design requirements entail the use of plastic for the enclosure and also need EMI-shielding, there are coatings available for EMI-shielding of the plastic enclosures.
For specialized equipment (like analyzers, medical equipment, X-ray machines) that emit high gamma or X-rays that need to be contained, lead(Pb) is a preferred choice of material for shielding.
Using metal enclosures that shield from EMI/RF however also means that a Faraday Cage is formed and useful wireless communication through radio frequencies is blocked too. To overcome this limitation, several techniques are used, like using an external antenna, multilayer antenna, hybrid antenna integrated into the enclosure (less commonly used) and using cleverly designed cut-outs in the enclosure that serve as antenna while maintaining the sleek aesthetic (example: in phones)
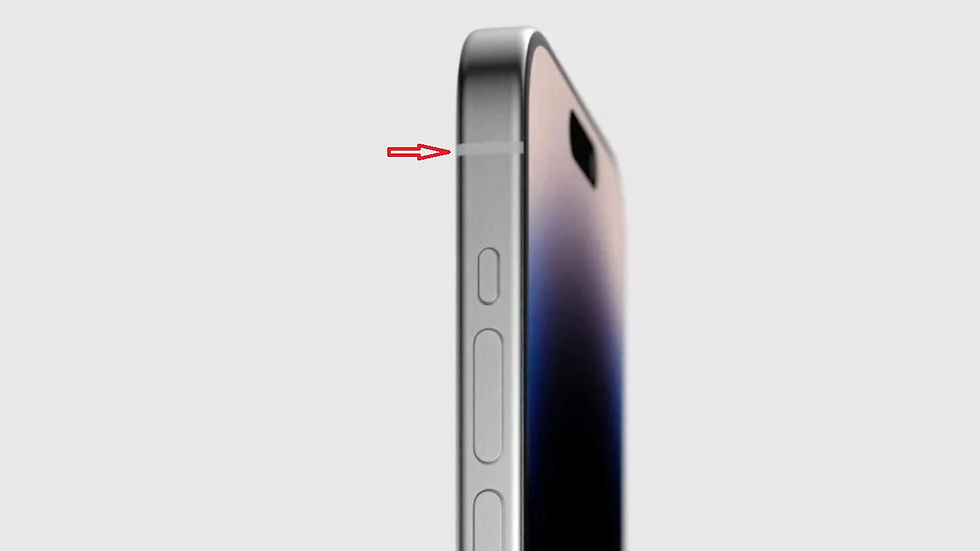
3. Thermal Management:
Effective thermal management is crucial for ensuring the reliability, longevity, and performance of electronic components.
To ensure safe operating temperatures by dissipating excess heat generated by the electronic components, adequate ventilation, heat sinks and fans are used in the enclosure.
Clever design techniques sometimes incorporate the use of materials like aluminum for the enclosure in such a way that the enclosure itself serves multiple purposes as a heat sink, for EMI shielding as well as providing good aesthetics, manufacturability and durability.
For extreme temperature environments outdoors, consider insulation to maintain stable internal temperatures.

4. Size and Form Factor:
The optimal size and form factor needs to be determined based on the dimensions of the electronic components and the intended use of the enclosure.
The enclosure should not be too large or too small compared to the internal components or assemblies and should suit the environment where the device needs to operate.

5. Ease of Use:
User-interface: The enclosure should be designed with user-friendly interfaces, including displays, buttons, and ports, to allow for easy access and interaction with the electronics. Well-designed labels for safety warnings and usage instructions marked on the enclosure allow better ease of use.
Accessibility: Where applicable, the enclosure should allow easy access to the internal components for repair, replacement or maintenance. This can be done through removable panels, hatches, doors etc. Efficient cable routing and management inside the enclosure allows for better accessibility and prevents cable damage.
Mounting: Suitable mounting options like wall mounts, DIN rails or rack mounts facilitate installation in various settings and better ease of use.
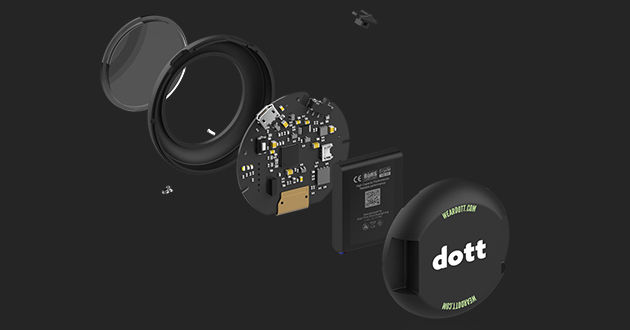
6. Safety Features and Regulatory Compliance:
Safety features such as tamper-evident seals, locks, and emergency shutoffs should be incorporated to protect users and prevent unauthorized access. Understand and adhere to industry-specific standards and regulations (e.g., UL, CE) that may apply to your electronic enclosure and provide appropriate labels and safety warnings for the correct usage of the device.
7. Ergonomics and Aesthetics:
Aesthetics play an important role for enclosure design in several industries like consumer electronics, medical devices, industrial equipment and more. Ensure that the enclosure design incorporates the company’s branding elements and is visually appealing to entice users.
Ergonomics plays a crucial role by focusing on the interaction between humans and products, ensuring that products are comfortable, safe, efficient, and user-friendly.

8. Cost Considerations:
Design aspirations need to be balanced with budget constraints, selecting cost-effective materials and manufacturing processes.
Using off-the-shelf components where possible can help in reducing development time and manufacturing costs. Innovative design solutions can also drastically reduce costs by using alternative designs that use cost-effective manufacturing processes to achieve the same functionality. For example, for aluminum enclosures, rather than using expensive CNC machining for making parts, alternative approaches that use extrusion process can be used to create the same functionality while drastically cutting down manufacturing costs.

In summary, designing electronic enclosures requires a comprehensive approach that considers environmental protection, material selection, EMI/RFI shielding, heat management, size and form factor, accessibility, cable management, modularity, safety features, durability, regulatory compliance, environmental impact, ergonomics, cost considerations, testing, documentation, and labelling. These considerations ensure that the enclosure effectively protects and supports the electronic components it houses while meeting the needs and expectations of users and regulatory authorities.
Comments